JWA (John Wayne Airport): One of Those Defining
Moments
January 20, 2009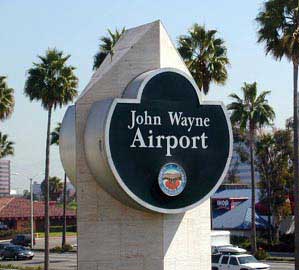
CALIFORNIA — John Wayne Airport (JWA),
a prominent, Los Angeles regional facility which is tightly surrounded
by high density commercial and residential areas and perched at the edge
of the Pacific Ocean, recently completed reconstruction of its primary
runway. Kimley Horn & Associates, Inc. provided project administration
and engineering while Butier Engineering, Inc. provided construction
management. The contractor, All American Asphalt, Inc., provided
construction supervision, materials, labor and equipment for the
building of the project
Primary work
included coring the top three inches of aged pavement on the 5,700 foot
main runway then re-paving the area with a PG 76-10 overlay.
Included in the specification was the requirement for protecting 68,000
square yards of runway shoulder and aprons with a protective coating
which was:
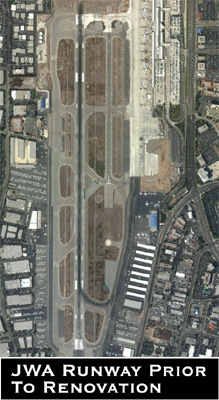
1. Waterborne
2. Environmentally clean (no VOC's, no HAP's, no toxins or
carcinogens and no PAH's)
3. Fuel resistant
4. 'Skid neutral'
or better
5. Insoluble to
rain within 1 hour of curing
6. Able to cure at
night @ 50°F in less than six hours
Those requirements set standards
that only new innovation could
solve, no product currently
existed that would meet these
guidelines.
Due to its
neighborhood proximity the Airport is regularly closed between the
hours of 11:00 p.m. and 6:00 a.m. This presented the challenge of
developing and installing a coating that could be placed and would
achieve full cure within this time window so heavy jet traffic could,
uninterrupted, perform all normal activities. Since the contract
penalty for interrupting normal JWA activities was $10,000 per
minute, the decision process for selecting a coating which met all
the requirements, especially those of the curing window was, to say
the least, characterized by heightened drama.
Ramsey Oil,
Inc. a division of All American Asphalt, Inc. would install the
coating. Paul Snow, Ramsey’s crew manager, was tasked with
coordinating night time field test applications of coating
alternatives; which were then evaluated by JWA representatives. After
considering many options provided through the All American management
team the head of procurement, John Todorovich, concurred with the JWA
representatives that the product supplied by Ecostar Science &
Technology, Inc. (a Lockheed Martin, Corp. spin-off) was the best
choice. That product was Carbon Plex H-25; manufactured under an
Ecostar license by Delta Trading, Inc. of Bakersfield, CA.
The
installation of the coating was scheduled for late December 2008 but
40°
F night time temperatures left little margin for error, i.e. the
Carbon Plex emulsion, which has exhibited the quality of fully curing
down to that temperature, had only been tested at John Wayne at night
time with 50°F
temperatures. The job was pushed to after the holidays with a “GO”
set for the evenings of January 8th and 9th.
Everyone was ‘antsy’ to wrap up this project after the months of
coating study; even if it meant going in the middle of the winter, at
night. The weather report for those dates was for rising temperatures
and clear skies, with possible ‘Santa Anna’ winds which would provide
excellent drying conditions. Everyone felt comfortable with pulling
off this last critical phase of the Project.
Seven thousand gallons of the
“Cold Cure” version of the Carbon Plex H-25 was prepared, then diluted
25% and shipped to the job site; ready to use. A light tower rigged,
2,000 gallon Bearcat distributor truck was readied, together with three
mobile light tower platforms. Against the back drop of jet engine roar
the Ramsey Oil crew put on their ‘game face’ and huddled in the staging
area at the pre-installation tailgate meeting with four JWA engineers
and two inspectors. Air and pavement temperatures were in the low 50's
F. The table was set for finishing the project except for one ‘fly in
the ointment’ - FOG. Wet fog was peppering the faces of all the men;
and there was not a flutter of a breeze to move it. The big question
was, “Should we scrub the mission or push on?” Paul Snow, who had the
most experience with the Carbon Plex felt a cautious start was possible;
paying close attention to the ‘break’ time. The plan was to install a
short run of the H-25, time the cure and then decide whether to ‘step on
the gas’ or scrub the effort for the night. Tension was high with
everyone’s blood pressure ramping up. The JWA engineers and inspectors
then present, huddled to consider the cautious start proposal, then
concurred with the All American crew manager; but their trepidation
could be summed up with one unnamed individual stating that “If this
application goes sideways you are going to see me hanging from the top
of that (nearby) 100 foot eucalyptus tree.”
At 10:45 p.m.
the gates were opened and the convoy of trucks was escorted out through
the fog hovering over the main runway.
As
the Carbon Plex H-25 does not need to be heated to cure under night time
conditions, minimal heat (110°
F) was used to encourage drying. At 11:07 p.m. the first twelve foot
swath began at 0.10-0.12 gal/sq yd spread rate. When the Bearcat
operator ‘dropped the hammer’ and disappeared into the fog on its first
mile plus run every eye at the start line leaned forward under the glare
of the light tower to glean information from the flow pattern and color
change of the freshly placed coating.
The entire span
of runway pavement surface had been saw cut with three eights inch deep
grooves at one inch on center. A special characteristic of the Carbon
Plex H-25 is its rapid 10:1 (static/shear thin) viscosity rise after
being pumped and sprayed. In less than one second from hitting the
pavement the static viscosity is nearly restored; assuring a significant
resistance to puddling in the grooves. On this foggy night it was
performing as designed, with virtually no uneven film thickness between
the pavement surface and the groove bottoms.
At this point
other good things began to happen. Before the Bearcat returned painting
its second twelve foot swath, a black hue began to show in the over
spray zone. The Carbon Plex emulsion was breaking!! Even with the
atmospheric vapor content above the surface being at or near saturation
the exothermic reaction designed into the “Cold Cure” version of H-25
was kicking in and forcing the micronized emulsion water component to
volatize. By the time the distributor truck returned a collective
“whew” had begun to set in. The blood pressures of about two dozen hard
working men were rapidly falling. Mental resignation letters were being
shredded. The JWA engineers granted that the installation could proceed.
By 1:45 a.m. the entire 640,000 s.f. was coated and curing at a
predictable pace. At about 3:30 a.m. the entire job was drivable; even
though the fog had actually worsened at times. No champagne was opened
but everyone associated with the effort felt as though it may have been
appropriate; as the first
critical stage of the job had been accomplished.
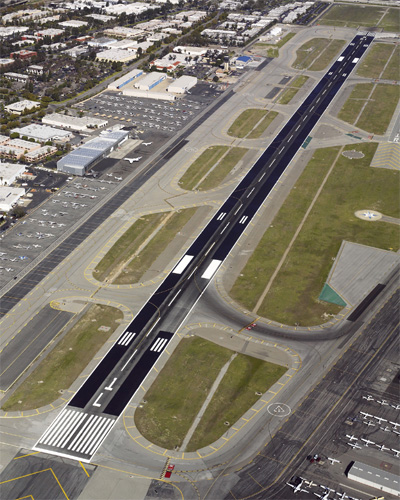
There are three
distinct stages to the life cycle of this type of pavement
preservation.
Stage
One had achieved complete
success. The coating was installed and cured in the allotted time and
under the conditions prescribed. Curing had progressed to a film
sufficiently tough to resist tire displacement as well as becoming water
fast with no chance of re-emulsification.
Stage
Two came the next morning
when all the ‘normal’ people who have jobs which allow them to stay at
home at night, could come out and witness the heavy jets trafficking
over the fresh, shiny black coating. Most importantly, like some clean
room entry mat, the jets then would roll over the three foot wide, white
thermoplastic stripe defining the runway, without one hint of any
tracking!! “Yeah team” could be read on the face of each early morning
inspector as they knew ‘they’ had made the right decision(s). The
performance was analogous to the test sites which, incidentally, were
done without the benefit of fog.
Stage
Three will be to watch the
product perform over the coming months and years; to see how well it
endures under the insult of hot jet exhaust, unspent J5 vapor, salty fog
and a hot Southern California solar bake.
While the
immediate reward is “No Penalties” there is also an intangible
yield to this type of project. That yield is the feeling of deep
satisfaction within every professional associated with this effort; of
thoughtfully and vigorously pushing the envelope and succeeding to
achieve against unusual challenges. We are also relieved to report that
the next morning’s sun brightly shone on the 100 foot tall eucalyptus
revealing no more weight in its branches than it bore the previous day!
William Coe
President, Ecostar Science and
Technology, Inc.
One of Those Defining Moments
There are instances when years of research and hard work
showcase innovations that will leave a large footprint,
moments that define a new era.
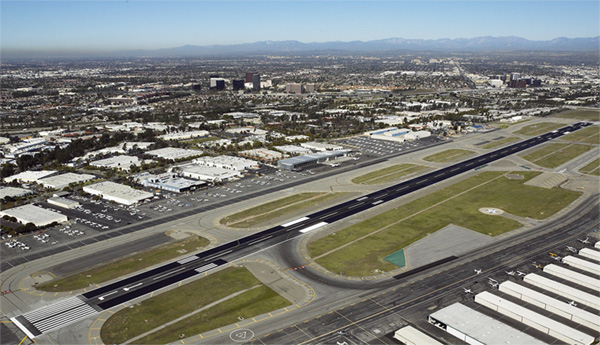
|